How Lean Helps These Big Brands
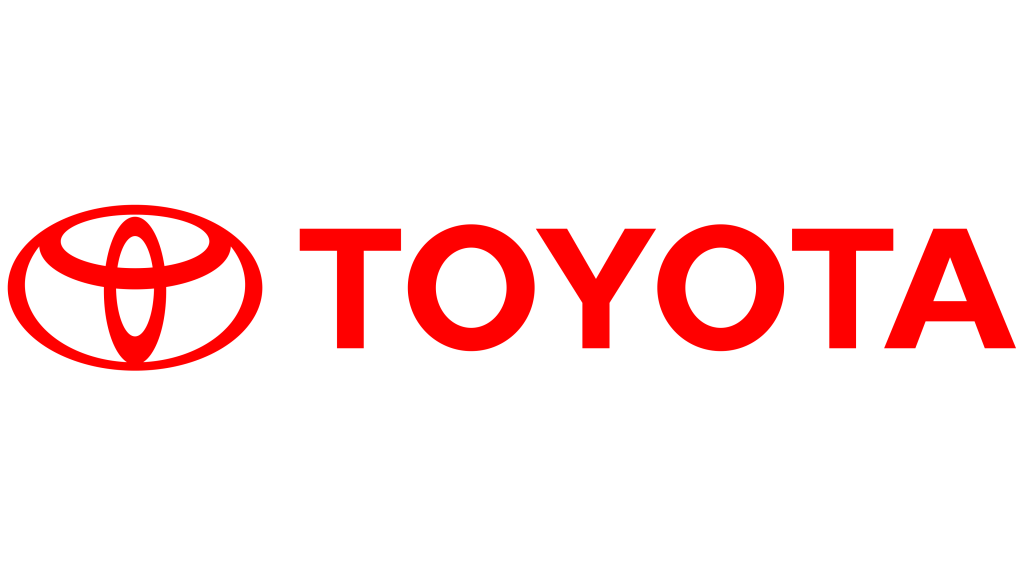
Toyota
Toyota is one of the pioneer companies to adopt Lean Management and has a successfully transitioned from a looms production company to a company producing automobiles.
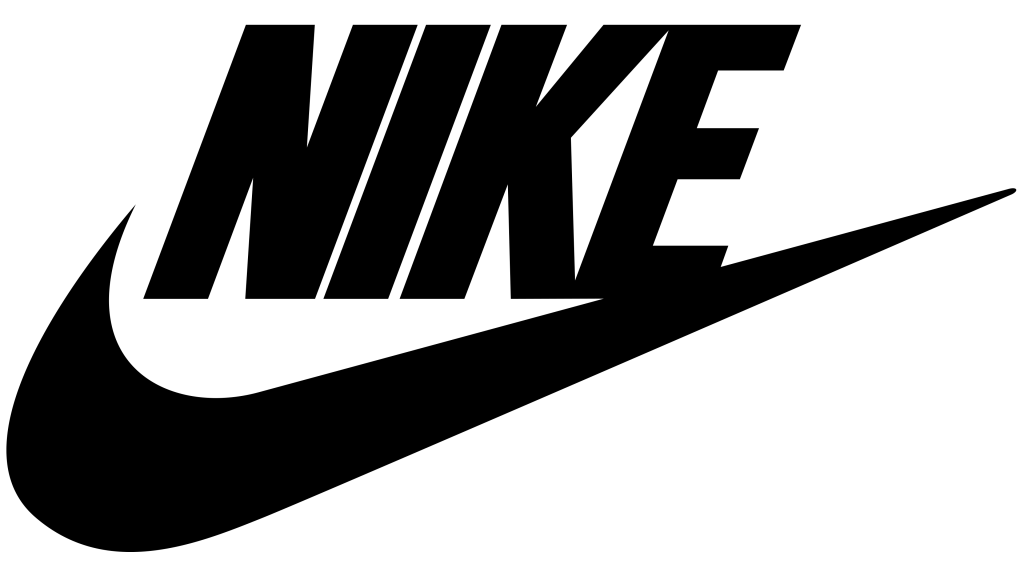
Nike
Using the power of Lean, they were able to transform the working conditions in their factories and reduced non-compliance to labour law by 15% in a short period of time.
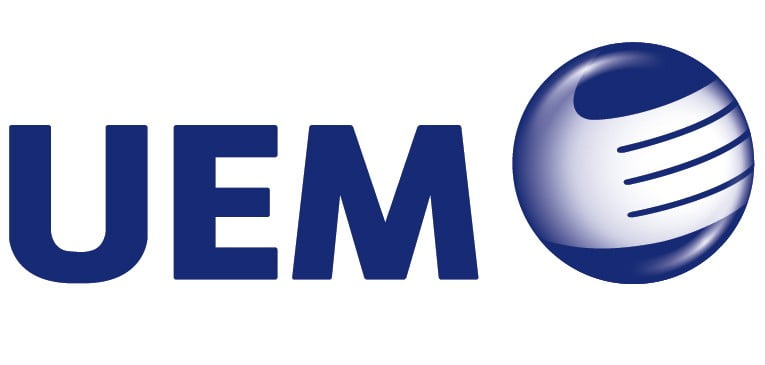
UEM
In efforts to increase growth and profitability, UEM Edgenta has their very own Lean Program. While focusing on healthcare and technology, they have already seen a jump in 21.8% of after-tax profit.